Pyramid's Quality Assurance Inspection Procedures
Process-Specific Checks
Extrusion
During extrusion, the cross sectional size of the extrudate is continuously measured by a laser micrometer as it exits the cooling bath. Dimensional tolerances have been established that meet or exceed the performance requirements for this type of product.
Cutting: Length Checks
Cutter operators are required to check cut belt lengths against a “check board” on a required frequency to assure that the cutter is functioning properly and belts are within the standard length tolerance.Welding: Visual Inspection of Welds
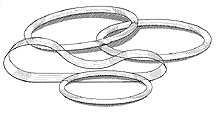
The shape and size of the weld flash (excess material created at the weld during the welding process) provides a visible indicator as to the quality of the welding operation. A belt from all welders is inspected at the beginning of each work period by the operator prior to going into full production. These startup belts are left for supervision to inspect, as well. During production, operators and supervisors make random checks throughout the welding process.
Grinding
After welding and further processing, belts are sent to the grinding area where the flash is removed. Each belt is individually inspected to see that the flash is the correct size and shape and if so the flash is removed by grinding so that the weld area is as close to the body size as is possible.Photographs of improper welds and flashes are posted in the grinding area to assist personnel in determining which belts are unacceptable. Unacceptable belts are placed in designated tubs for recycling.
Previous Page--Pre-Acceptance Testing
Next Page--Tensile Strength Tests